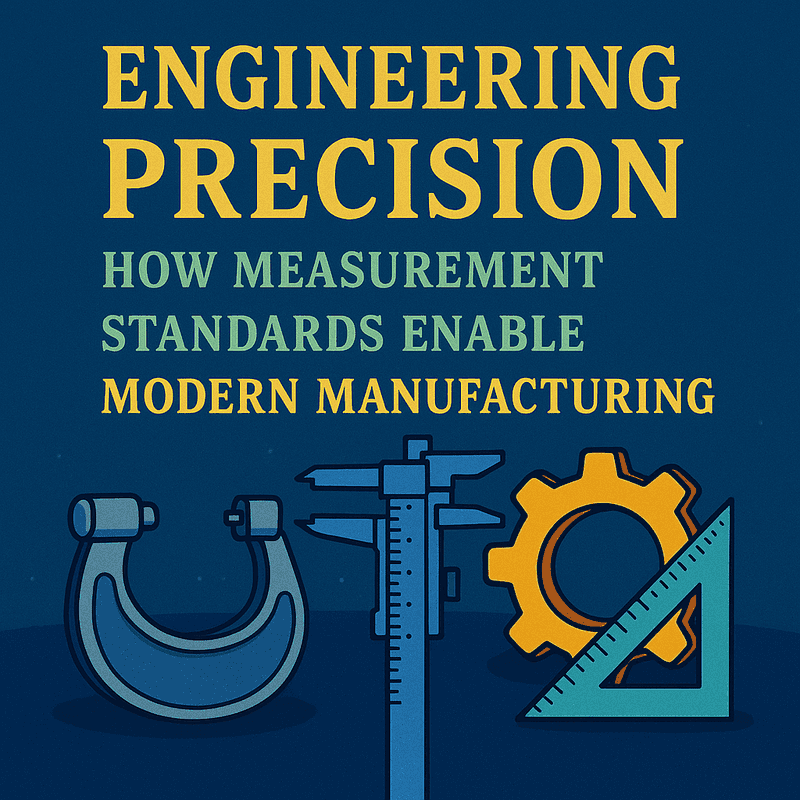
Modern engineering and manufacturing depend on an invisible but essential foundation: precise measurement standards. From the microchips in our smartphones to the engines in our cars, from the bridges we cross to the satellites orbiting Earth, every engineered product relies on measurement systems that are accurate, consistent, and traceable.
The precision required in modern manufacturing is astonishing. Computer chips are manufactured with features smaller than a virus, aircraft engines must operate within tolerances of thousandths of an inch, and medical devices must function reliably for years. This level of precision would be impossible without sophisticated measurement systems and international standards.
The Foundation of Interchangeability
One of the most important concepts in modern manufacturing is interchangeability—the idea that parts made in different factories, by different companies, or at different times can fit together perfectly. This concept, which revolutionized manufacturing in the 19th century, depends entirely on precise measurement standards.
Before the development of standardized measurements, every part had to be custom-fitted. A bolt made in one workshop might not fit a nut made in another, even if they were intended to work together. This made mass production impossible and repairs difficult and expensive.
The development of standardized measurement systems, particularly the metric system and its derivatives, enabled the creation of interchangeable parts. Today, a bolt manufactured in Germany can fit a nut made in Japan, and both can be used in a product assembled in the United States. This global standardization has been essential for the development of modern supply chains and international trade.
Quality Control and Metrology
Quality control in modern manufacturing relies on sophisticated measurement systems that can detect variations far smaller than the human eye can see. These systems use a variety of techniques, from simple calipers and micrometers to advanced coordinate measuring machines (CMMs) and optical measurement systems.
Coordinate measuring machines are among the most precise measurement tools used in manufacturing. These devices use probes to measure the dimensions of parts with accuracy of a few micrometers (millionths of a meter). They can measure complex three-dimensional shapes and compare them to digital models to ensure they meet design specifications.
Optical measurement systems use cameras and sophisticated software to measure parts without physical contact. These systems can measure large numbers of parts quickly and are particularly useful for quality control in high-volume manufacturing. They can detect surface defects, measure dimensions, and verify that parts meet design tolerances.
Semiconductor Manufacturing
Perhaps no industry demonstrates the importance of precise measurement more than semiconductor manufacturing. Modern computer chips contain billions of transistors, each with features measured in nanometers (billionths of a meter). Manufacturing these chips requires measurement and control systems that can operate at the atomic level.
The manufacturing process for computer chips involves hundreds of steps, each requiring precise measurement and control. Photolithography, the process of transferring circuit patterns onto silicon wafers, requires positioning accuracy of a few nanometers. This is equivalent to hitting a target the size of a virus from a distance of several kilometers.
Measurement systems in semiconductor manufacturing must operate in clean room environments where even a single dust particle can ruin a chip worth thousands of dollars. These systems use advanced optics, lasers, and electron microscopes to measure and control the manufacturing process with extraordinary precision.
Aerospace Engineering
Aerospace engineering represents another field where measurement precision is critical. Aircraft and spacecraft must operate in extreme environments while maintaining safety and reliability. Every component must be manufactured to exact specifications and thoroughly tested to ensure it will perform as expected.
Aircraft engines, for example, operate at temperatures and pressures that would destroy most materials. The tolerances for engine components are extremely tight—often measured in thousandths of an inch. A single measurement error could result in engine failure, potentially causing a catastrophic accident.
Spacecraft face even more demanding requirements. They must operate in the vacuum of space, exposed to extreme temperatures and radiation. Every component must be precisely manufactured and tested to ensure it will function reliably for years or decades without maintenance.
Medical Device Manufacturing
Medical device manufacturing requires precision that can literally mean the difference between life and death. Implants, surgical instruments, and diagnostic equipment must be manufactured to exact specifications to ensure they function correctly and safely.
Hip and knee implants, for example, must fit precisely within the patient's body. Even small variations in size or shape can cause pain, reduced mobility, or implant failure. Manufacturing these devices requires measurement systems that can detect variations of a few micrometers.
Surgical instruments must be manufactured with extreme precision to ensure they perform correctly during procedures. Scalpels, forceps, and other instruments must have the exact dimensions and properties specified by their designers to ensure they function safely and effectively.
Construction and Infrastructure
Large-scale construction projects also depend on precise measurement systems. Skyscrapers, bridges, and other major structures must be built to exact specifications to ensure they are safe and functional. Even small errors in measurement can result in structural problems that could lead to catastrophic failure.
Modern construction uses advanced measurement technologies including GPS, laser scanning, and 3D modeling to ensure accuracy. These technologies allow construction teams to work with precision that would have been impossible just a few decades ago.
Bridge construction, for example, requires precise measurement of distances, angles, and loads. The components of a bridge must fit together perfectly, and the entire structure must be able to support the loads it will carry throughout its lifetime. Measurement errors could result in structural failure with potentially catastrophic consequences.
The Future of Engineering Precision
As manufacturing technology continues to advance, the demand for ever more precise measurement systems will grow. New materials, new manufacturing processes, and new applications will require measurement capabilities that are currently beyond our reach.
Quantum measurement systems, which use the principles of quantum mechanics to achieve unprecedented precision, may revolutionize manufacturing in the coming decades. These systems could enable measurements at the atomic level, opening new possibilities for manufacturing and materials science.
The development of new measurement standards and the improvement of existing ones will continue to be essential for technological progress. As we push the boundaries of what is possible in engineering and manufacturing, our ability to measure and control the processes involved will become even more critical.
The story of engineering precision is more than just a technical history—it's a testament to human ingenuity and our relentless pursuit of excellence. From the first standardized parts to the quantum measurement systems of the future, each advance in measurement technology has enabled new possibilities in engineering and manufacturing.
As we continue to develop new technologies and push the boundaries of what is possible, precise measurement will remain the foundation upon which all engineering and manufacturing depends. The future of technology depends on our ability to measure and control the world around us with ever greater precision and accuracy.